Order Scheduling
There are two standard ways to manage orders: Manual Scheduling, and Automatic Scheduling. These differ mainly in the way that the orders are planned. You can mix the scheduling types within your network with manual scheduling in some areas and automatic scheduling in others.
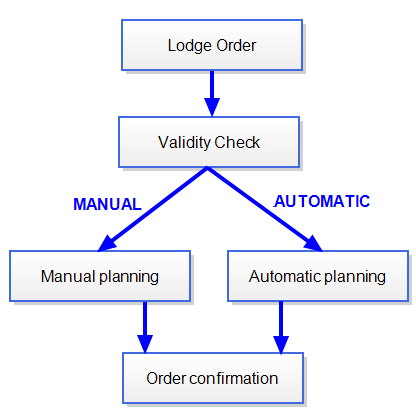
Order lodging process under manual and automatic scheduling
Order lodging process under manual and automatic scheduling
Manual Scheduling
With manual scheduling, the system checks that the order is valid but does not check the system capacity and does not schedule the orders. A planner must schedule the orders by creating and finalising a plan that includes those orders. The planner is responsible for ensuring that there is sufficient capacity in the system to supply the orders.
See the Plan History Module for more information about manual planning.
Automatic Scheduling
With automatic scheduling, the system checks that the order is valid and immediately checks to ensure that there is capacity to deliver the order. If there is, the order is confirmed and scheduled. If not, the customer can be advised of the problem and prompted to change the order.
Partial Scheduling
Partial scheduling is a mixture of manual and automatic scheduling. In partial scheduling, DMS performs a capacity check as for automatic scheduling, but a planner can still move the orders before they are scheduled and confirmed.
Partial planning is not widely used and is not covered in any detail in this manual.
Which ordering system should you use?
Manual scheduling is more flexible, but automatic scheduling is more efficient.
- Manual scheduling allows you to consider practical or business related factors when scheduling orders. For example, you may need to set limits on when orders are delivered, or you may want to deal differently with certain customers.
Example
Manual scheduling is typically used when regulators or outlets in the area are under manual control. In this case, it is important to minimise the number of changes to regulator flow, and to control the timing of the flow changes, because a field officer must visit the regulator in person to make each change.
- Automatic scheduling allows customers to lodge orders at shorter notice and to receive immediate confirmation of the order. Orders are dealt with on a first-come first-served basis.
Example
Automatic scheduling is typically used where regulators and outlets are under automatic control and customers are using web, mobile or IVR systems to manage their own orders.